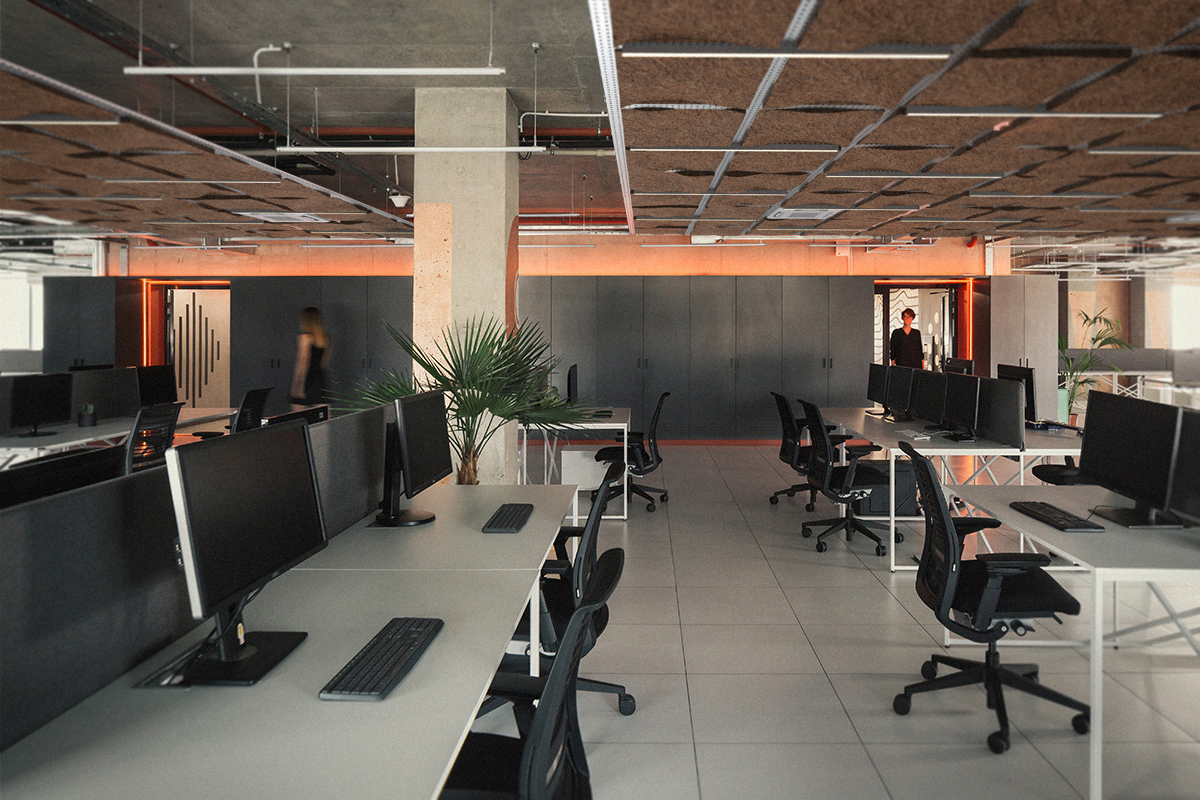
Acoustic Coconut Fiber Panel
2020
>>>Recognition: 2020 James Dyson Award, The Outstanding Works Award, China’s Region
Introduction
Acoustic Coconut Fiber Panel is a sustainable-material-driving project. It starts with the research of a natural material, one of the byproducts of the food industry: coconut fiber. Based on the property of fibrosis, I establish the ideation of using coconut fiber as the alternative material for sound-absorbing products. Throughout researching on the manufacturing process and experimenting prototypes, I decided to design an acoustic panel which can be assembled in interior space. Then I turn the project into the form study. I study the factors of designing the acoustic board from the specific texture of professional sound-absorbing products. Then I create the connection between the undulant form with the location where the coconuts are from - the cozy coast of South Asia. Finally, it turns out a natural, relaxing, and breathing style acoustic panel.
Research
>>>About Synthetic Fibers
Synthetic Fibers including mineral wools and glass fibers are widely used in interior space to achieve the sound-absorbing function. The interspaces between fibers cause the inhomogeneous density that efficiently weakens the conduction of sound wave. These fibers are usually made into the form of panels and be assembled around the interior space to absorb sound and weaken the sound reflection.
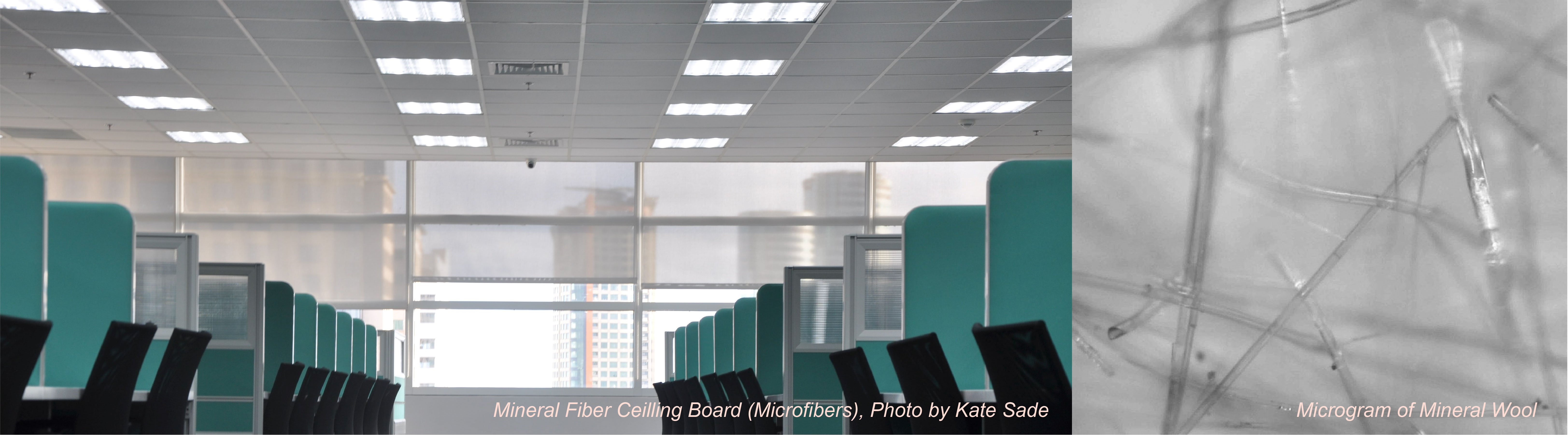
However, these synthetic fibers will peel off microfibers during the process of aging in which has the potential health risk to people who are long-term working in this space. Besides, these artificial materials produce noxious gases like methanal because of the great amount of using of chemical materials during the manufact during the process.
In short, an alternative material that is more health-friendly is needed.
>>> About Coconut Fibers
The Coconut Fibers (coir) is a natural fiber extracted from the outer husk of coconut and used in products such as floor mats, doormats, brushes, and mattresses. Coir is the fibrous material found between the hard, internal shell and the outer coat of a coconut.
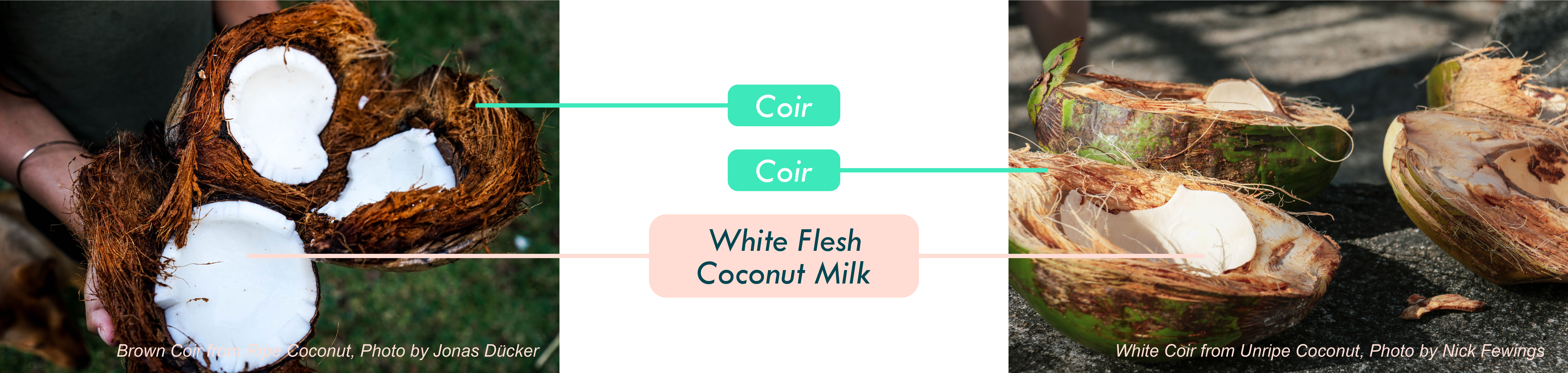
In the Food Industry, people only use coconut meat and coconut milk. Throughout the food production process, it leaves the coconut coir as the byproducts in a considerable number. Regularly, the coconut fibers are made into baskets, carpets, and gardening material. They all base on the properties of fibrosis, waterproof, and strength.
As a natural material, the coconut fibers have the primary feature of fabric, and this feature reminds me the similarity with the sound-absorbing materials, especially mineral fiber. Then I go into the material research to verify the possibility of using coconut fibers as the alternative material for synthetic fibers.
Material Research
The Sound Absorption Applications of natural fibers have been studied and tested by number of papers and experiments. By researching those papers, I collect information about how coconut fiber performs about its acoustic characterization, and the optimal material formula.
>>> The Acoustic Performance Comparison
Synthetic Fibers including mineral wools and glass fibers are widely used in interior space to achieve the sound-absorbing function. The interspaces between fibers cause the inhomogeneous density that efficiently weakens the conduction of sound wave. These fibers are usually made into the form of panels and be assembled around the interior space to absorb sound and weaken the sound reflection.

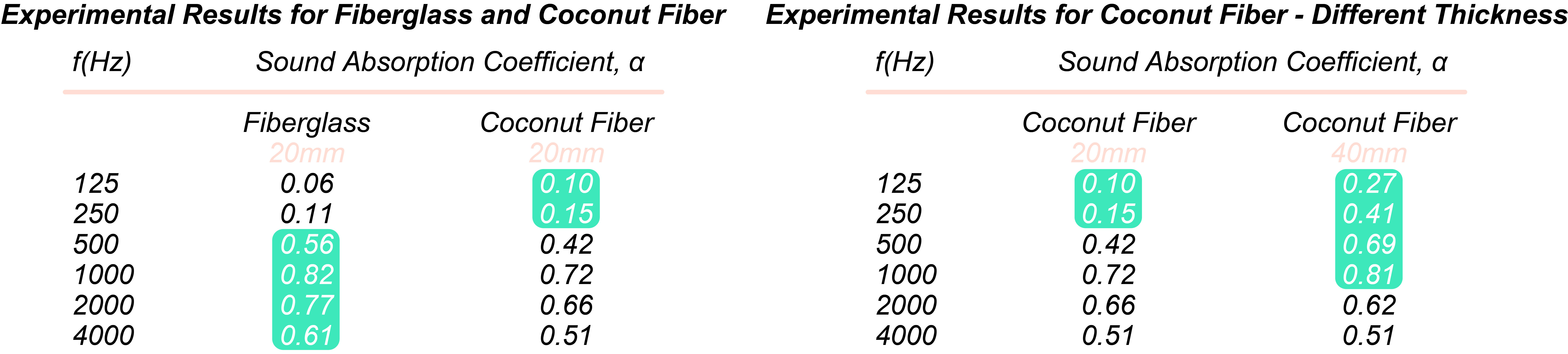
In This Experiment, the coconut fiber panels and the glass fiber panels are set in an equal reverberation room to test the capability of weakening the reflection of the sound wave. Both coconut fiber panels and glass fiber panels are in the same size and thickness- 20mm thickness and 6m2 area. As the result, the coconut fiber panels perform better sound absorbing capability under the frequency of 250Hz. By changing the thickness of coconut fiber panels for the control group experiment, the extension of the range shows that the thickness remedy the acoustic performance to a certain extent.
Besides, the average frequency of a person speaking is between the range of 85 to 255 Hz. So the coconut fiber panels can satisfy the acoustic requirement in unspecialized space.
>>> Material Performance Experiment
The Sound Absorption Properties of coconut fiber panels are influenced by several factors including additional materials and textures. This experiment uses the impedance tube to mrasure the sound absorption performance of the samples.
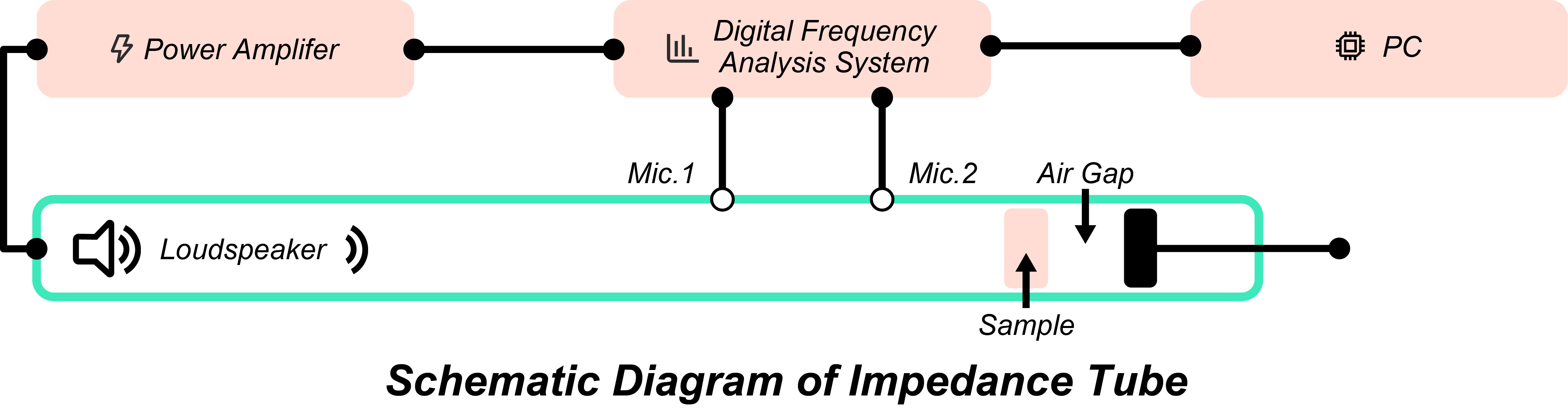

Several Samples with different material ratios are tested in the impedance tube. The PU foam is added to coconut fiber in order to transform the form of interspace inside the material. Also, the PU foam helps to shape the coconut fibers through the process of making samples. The range of the frequency used in the impedance tube testing was from 1 Hz to 5000 Hz. By analyzing the sound absorption coefficient, it shows different results for different samples.
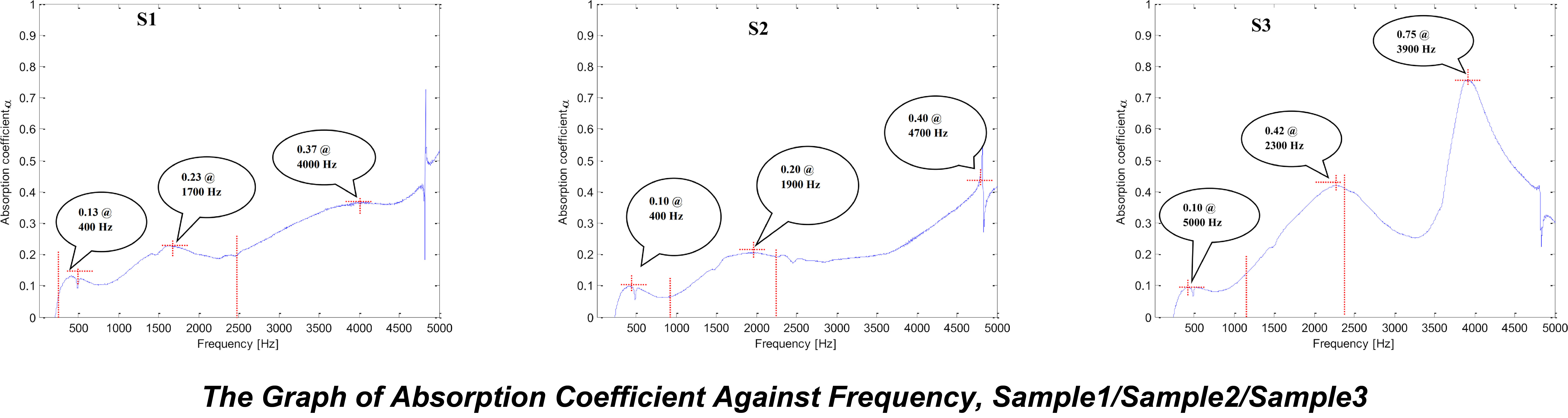
Evidence from this study suggests that the most suitable sample that can be used as an acoustic panel is sample 3 which have 0.75 of the absorption coefficient value between the frequencies of 3500 to 4000 Hz.
Prototypes
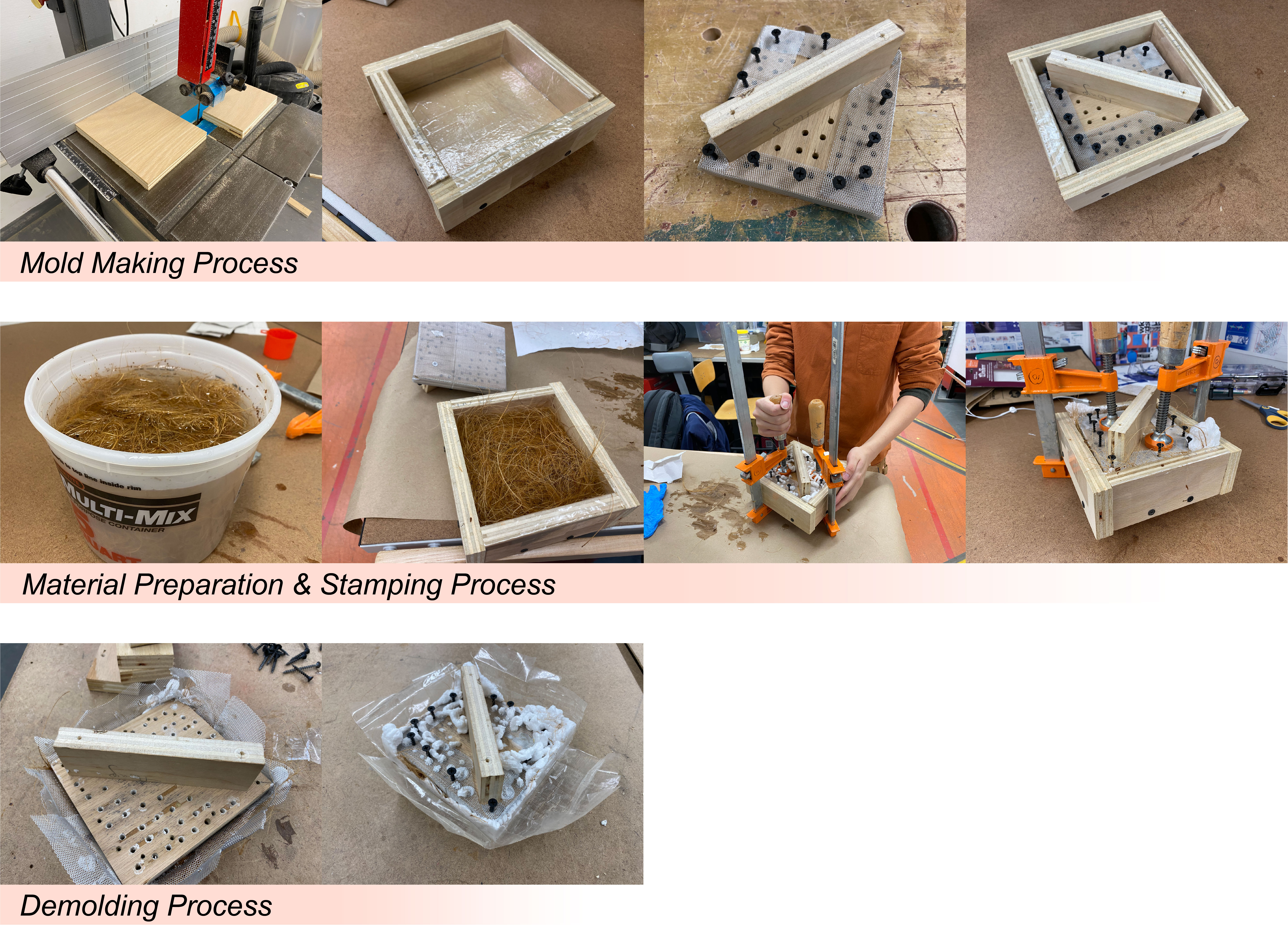
By Referring to the experiment process from the previous paper, I set my experiment stamping the coconut fibers with PU (polyurethane) foam. I first make the mold with wood board, barbed wire (demolding), and waterproof tape. Then I boil the coconut fibers in order to clean them and make them more shapable To simulate the pressure of the manufacturing process, I use clips to squeeze the mold. After 8 hours of drying, I dismantled the coconut fiber panel out of the mold.
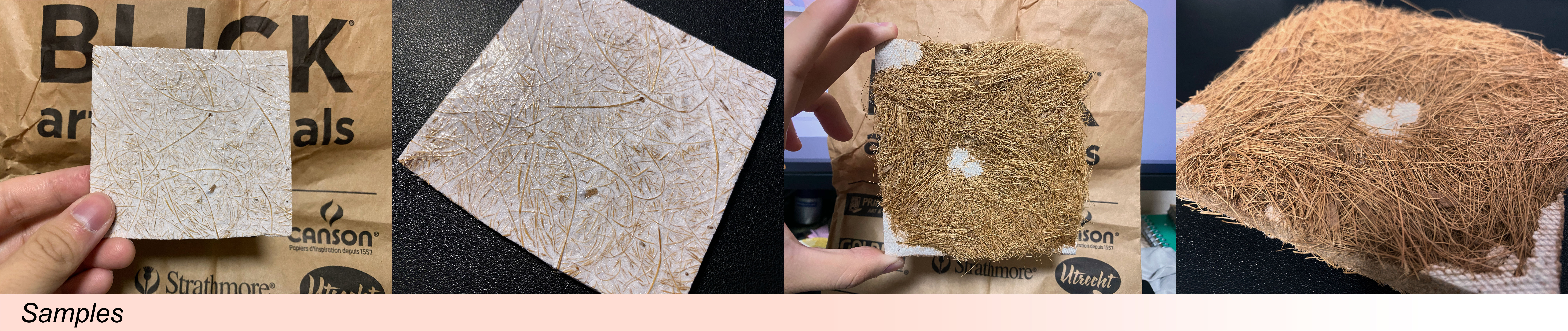
The Result shows two Samples with different volume ratios of coconut fibers and PU foam.
Manufacturing Study

In the Industrial Manufacturing, the process of making coconut fiber products like gardening pots are pressing pure coconut fibers with 1000kg strength and 100C temperature at the same time. Because the coconut fibers itself (without additional material like PU) can support the requirement of daily use. Based on the sustainable development goals, I decided to design the acoustic coconut fiber panel with pure fibers.
Form Study
>>> Acoustic Form Study
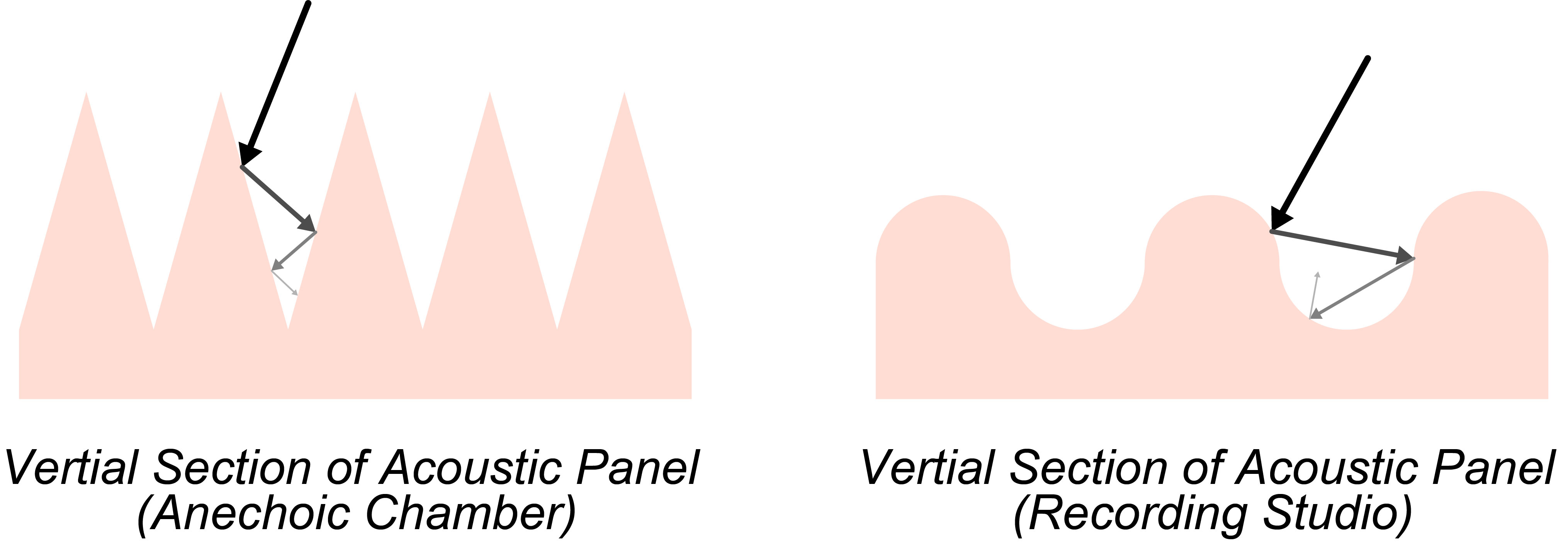
The Existing Acoustic Products reflect a form feature for sound-absorbing function. The anechoic chamber is assembled with the sharp-shape sound-absorbing panel. The angle of the shape will reflect the sound into the bottom, and the material weakening each time of the reflection. As the shape becomes more curved, the absolute ability to absorb will decrease, it also fits the daily needs of the sound reflection.
Different shapes also bring a different feeling to the user. As the main idea of the acoustic coconut fiber is a nature-material product, the origin of the coconut - the tropical coast inspires me that I can design a form that can bring a feeling of breathing. This form also creates a conflict with a monotonous urban interior environment. Therefore, this relation brings a fresh experience for the user of this space.
>>>Design
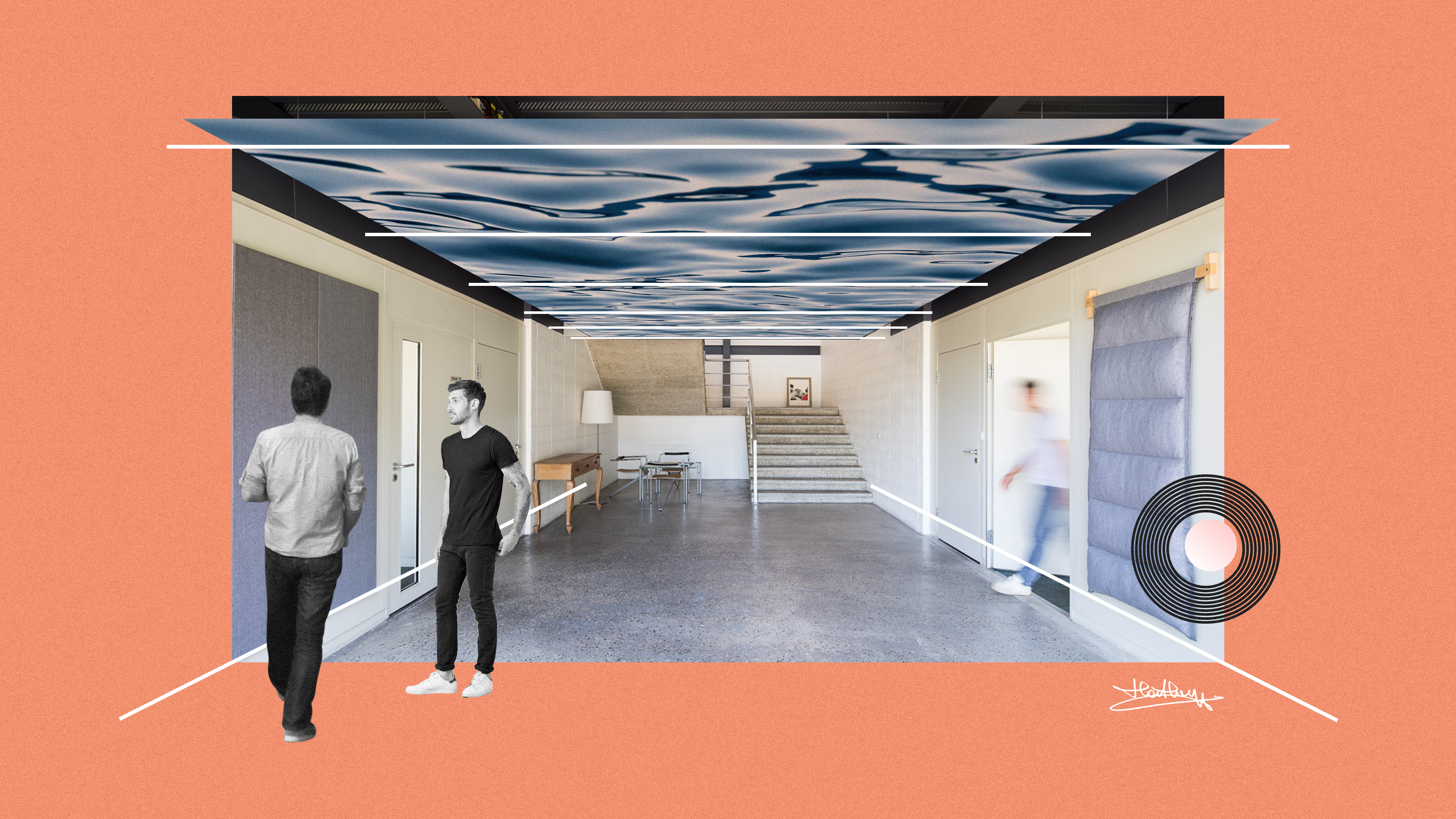
The Element of waves of the ocean is abstracted to be the feature of the form design. In order to imitate this form, I look up some mathmetic analyzation such as interference /superposition, and model some pieces in software. Also, I use the method of image capture to create more random forms.
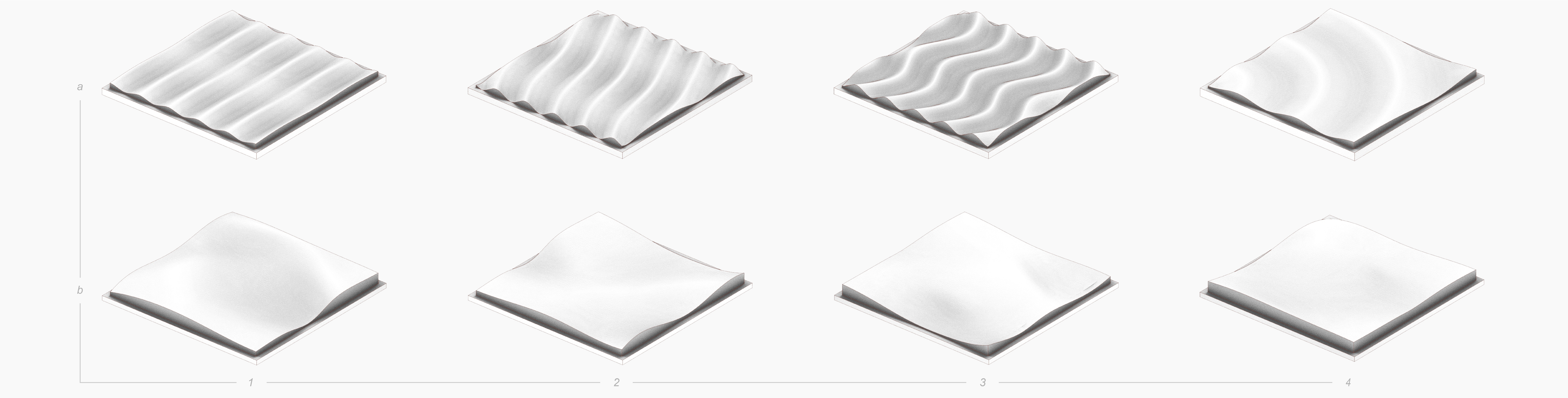
When the regular forms (a1/a2/a3/a4) are assembled by numbers, the surface shows a repetitive feature which is against the original ideal effect. So I chose the more irregular forms (b1/b2/b3/b4) as a suite. When putting different sides together, four types of panels could assemble infinite possibilities.
>>>Assembly
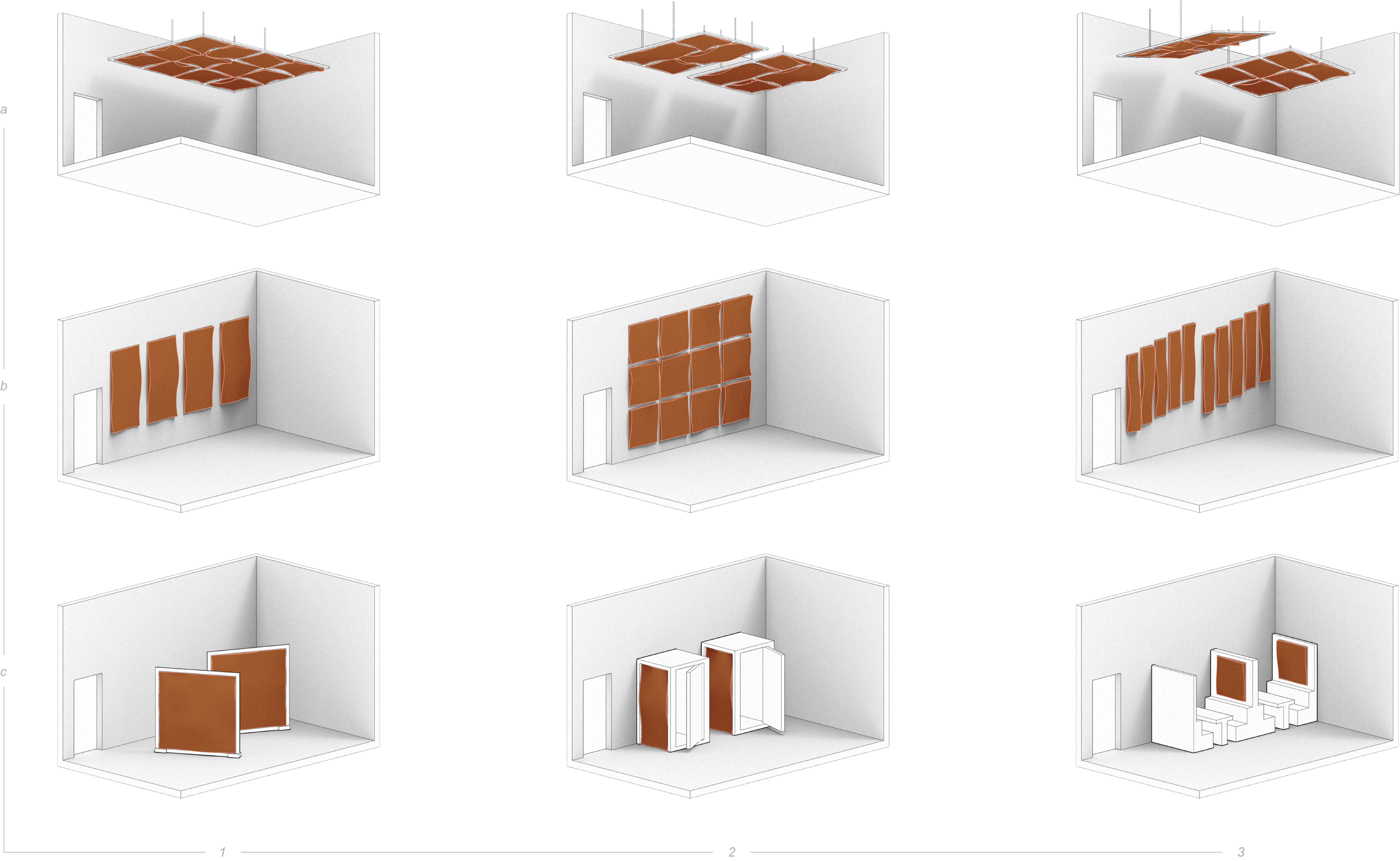
More Assemblies are desgined to install acoustic coconut fiber panels differently.
a1: Square Shape, Ceiling Assembly
a2: Rectangle Shape, Ceiling Assembly
a3: Diagonal Frame, Ceiling Assembly
b1: Rectangle Shape, Wall Assembly
b2: Mosaic Shape, Wall Assembly
b3: Terrace Rectangle Shape, Wall Assembly c1: Byobu Assembly
c2: Phone Booth Assembly
c3: Seat Assembly
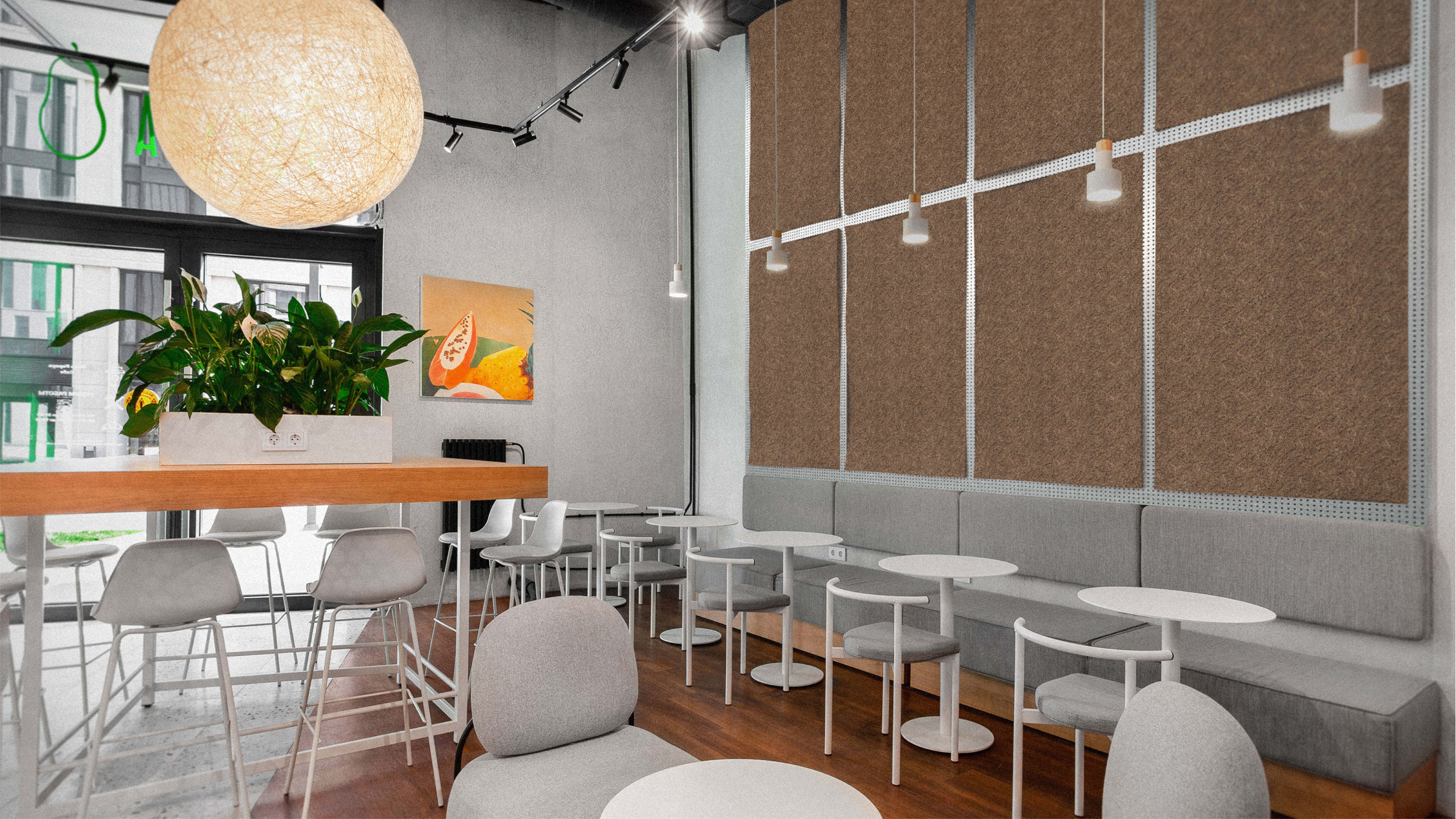
Future Developments
The Acoustic Coconut Fiber Panel still has space for future design and faces several difficulties which needs to be solved:
(1) The material still needs to be improved to achieve the standard of the interior products including fireproof.
(2) New patterns and assemblies can be designed to create a different style for different spaces.
(3) On the manufacturing side, a new supply chain is required to be organized for the non-traditional product.
(4) On the business side, there are difficulties to stimulate consumers’ motivation to accept and use innovative products.